In industries where water usage is pivotal, such as power plants, oil refineries, and chemical manufacturing, the integrity of industrial systems is constantly challenged by scale formation and corrosion. This challenge necessitates the employment of advanced scale and corrosion inhibitors, ensuring not only efficiency but also financial viability by prolonging equipment lifespan.
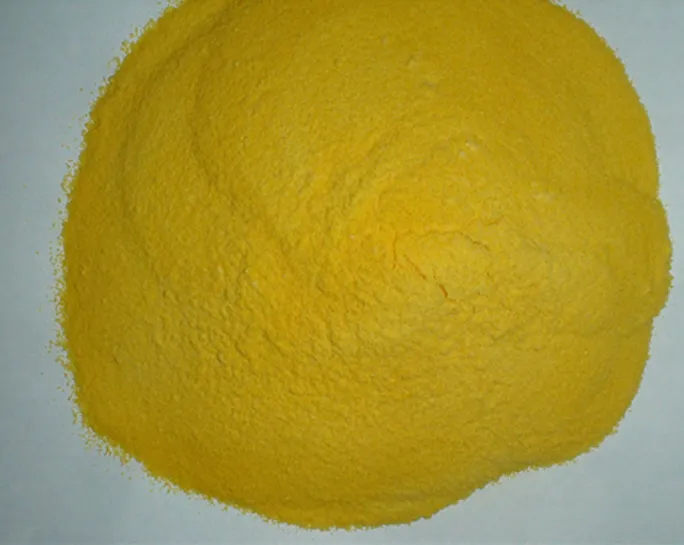
Scale and corrosion inhibitors are specialized chemicals designed to mitigate two prevalent industrial issues the buildup of mineral deposits, known as scale, in water systems, and the corrosive deterioration of metal components.
Understanding and selecting the right inhibitors is critical for maintaining operational integrity and efficiency.
Experience shows that the efficacy of these inhibitors hinges on several crucial factors, including water chemistry, temperature, and the materials of the system. For instance, in a high-temperature environment typical of power plants, the scale formation accelerates, necessitating inhibitors that can withstand harsh conditions. It's crucial to customize inhibitor solutions to meet specific operational parameters—a one-size-fits-all approach can be both economically wasteful and technically ineffective.
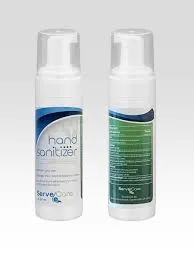
From a professional standpoint, the scope of expertise involved in the deployment of scale and corrosion inhibitors spans chemistry, material science, and engineering. Chemically, these inhibitors often consist of polymers, phosphonates, or phosphates, each type suitable for different industrial settings. Polymers work by dispersing scale-forming minerals like calcium carbonate, preventing their crystallization and deposition on equipment surfaces. Phosphonates provide a dual function—chelating metal ions to prevent scale and forming protective films that minimize corrosion.
scale and corrosion inhibitor
Investing in premium scale and corrosion inhibitors demonstrates not only an acknowledgment of their expert design and formulation but also a commitment to sustainable industrial practices. Effective inhibitors contribute significantly to water and energy conservation, aligning with global sustainability goals. They reduce the need for frequent water system cleaning and maintenance, thereby conserving water and energy otherwise required for waste processing and equipment downtime.
An authoritative source in the field, the National Association of Corrosion Engineers (NACE), emphasizes the importance of systematic monitoring and maintenance protocols alongside the use of inhibitors. Regular monitoring allows for the early detection of issues, while maintenance ensures that inhibitor solutions remain effective over time. By adhering to guidelines from such respected organizations, companies can enhance the trustworthiness of their operational practices.
Trust in scale and corrosion inhibitors is further substantiated by rigorous testing and certifications, ensuring they meet industry standards. ISO certifications and ASTM standards are benchmarks that products should ideally bear, signaling their reliability and safety. Trust is not only about product performance; it's about ensuring that these solutions are environmentally compliant and non-hazardous, thus safeguarding human health and the surrounding ecosystem.
In conclusion, the strategic selection and application of scale and corrosion inhibitors are paramount in safeguarding equipment and boosting industrial efficiency. They should be seen as indispensable tools in the arsenal of industrial maintenance, backed by experience, expertise, authority, and trust. By integrating these inhibitors into water management systems, industries can achieve considerable cost savings, improved operational reliability, and adherence to environmental standards—ultimately supporting a healthier bottom line and planet.