Scale and corrosion inhibitors are indispensable in a myriad of industries, primarily in oil and gas, water treatment, and manufacturing. These chemicals play a critical role in preserving the integrity of machinery and piping, thus extending their lifespan and maintaining operational efficiency. Understanding the complexities behind these inhibitors can enhance one's ability to select the appropriate product for specific processes, ensuring maximum protection against scale and corrosion.
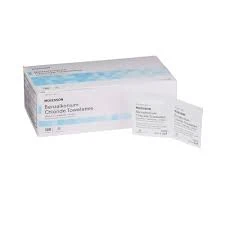
The basic function of scale inhibitors is to prevent the formation of mineral deposits on equipment surfaces, which occur naturally in water systems through the evaporation and concentration of solubles. Common troublesome scales include calcium carbonate and sulfate, barium sulfate, and silica. These deposits can impair system efficiency, leading to increased energy consumption and maintenance costs. On the other hand, corrosion inhibitors protect metal surfaces from the oxidative reactions that break down metals, causing leaks and equipment failure.
One line of defense against scale formation involves the use of threshold inhibitors, which effectively disrupt the crystal growth of scale-forming minerals. For instance, phosphonates, a type of threshold inhibitor, are widely recognized for their efficacy in controlling calcium carbonate scale due to their ability to adsorb onto calcium carbonate crystal surfaces, thus halting their growth. These inhibitors can handle high-hardness water conditions, making them essential for industrial and municipal applications.

Chelating agents and dispersants also serve as significant players in scale control. Chelating agents, like EDTA, bind metal ions in solution, which prevents them from forming precipitates. Dispersants, however, function by keeping potential scale particles suspended in the fluid, allowing them to be removed easily through filtration. This dual mechanism ensures that scale formation is not simply retarded but effectively managed, reducing operational downtimes and boosting productivity.
When it comes to corrosion inhibitors, several classes are available depending on the nature of the metal and the environmental conditions. Organic compounds such as amines and azoles are popular choices due to their ability to form protective films over metal surfaces, thereby minimizing direct contact between the metal and corrosive agents. In contrast, inorganic inhibitors, like nitrites and silicates, create a passive film by reacting with the metal surface, which significantly decreases oxidation rates.
scale and corrosion inhibitor chemicals
The application of bimetallic systems, where different metals are joined, presents unique challenges in corrosion management that are effectively managed by mixed inhibitors. These formulations combine properties of several individual inhibitors to address a spectrum of scale and corrosion problems.
Success in employing scale and corrosion inhibitors is often determined by their correct dosage and application method. Over- or under-dosing can lead to suboptimal performance and unnecessary environmental burden. Real-time monitoring systems offer a sophisticated approach to scaling and corrosion management. By continually analyzing water chemistry and environmental conditions, these systems ensure that precise inhibitor quantities are applied, maximizing the efficacy of the treatment regime.
As industries strive toward sustainability, the environmental impact of scale and corrosion inhibitors has gained prominence. The development of biodegradable and less toxic formulations is accelerating, addressing both industrial needs and environmental concerns. Companies that harness such innovations not only improve their operational efficiency but also enhance their standing in an increasingly eco-conscious marketplace.
The choice of an appropriate inhibitor involves not only a detailed understanding of chemistry but also of the operational nuances of the specific system. Leading manufacturers collaborate with industrial experts, conducting extensive field testing to tailor products to specific applications. This commitment to expertise and trustworthiness is a critical factor in navigating the ever-evolving landscape of industrial chemistry solutions.
In conclusion,
scale and corrosion inhibitors are essential components in the maintenance of industrial systems. By carefully selecting, applying, and monitoring these chemicals, industries can achieve both operational excellence and sustainable practices. As technology advances, the synergy among industry expertise, innovative chemistry, and environmental stewardship will undoubtedly shape the future of this vital sector.