Flocculants are essential in various industries, particularly in water treatment, where they facilitate the aggregation of suspended particles. Understanding the different types of flocculants is crucial to optimizing treatment processes, ensuring environmental compliance, and enhancing operational efficiency.
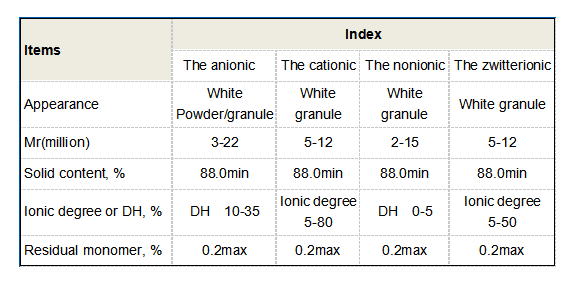
Flocculants fall into several categories based on their chemical composition, molecular weight, and charge type. Each type is designed for specific applications and conditions. Here's an in-depth look at the various types available and their applications.
1. Inorganic Flocculants
These are typically metal salts like aluminum sulfate (alum) and ferric chloride. Inorganic flocculants are widely used due to their effectiveness and cost-efficiency. They work by neutralizing the charges on suspended particles, allowing them to clump together. Inorganic flocculants are especially beneficial in municipal water treatment plants and are adept at handling high-turbidity waters.
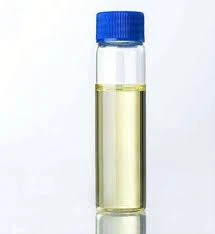
2. Organic Flocculants
These are primarily polymers such as polyacrylamides. Organic flocculants are effective in smaller doses compared to inorganic ones, reducing sludge volume. They are designed to target specific contaminants, offering tailored solutions for industrial processes. Acrylamide-based flocculants are popular in mining and mineral processing, where they facilitate the separation of ores from sediments.
3. Cationic Flocculants
These positively charged flocculants are particularly effective in treating negatively charged particles. Cationic flocculants are prevalent in wastewater treatment, especially in removing oils and organic matter. Industries such as food processing and paper manufacturing favor cationic flocculants for their efficiency in clarifying and thickening processes.
4. Anionic Flocculants
Anionic flocculants, bearing a negative charge, are used to treat positively charged particles. They prove invaluable in applications requiring the flocculation of fine particles, such as in the sand and gravel industries. These flocculants are also critical in sludge dewatering, improving the sedimentation process and easing disposal challenges.
different types of flocculants
5. Nonionic Flocculants
These are polymers without any charge, offering versatility across various pH levels and ionic environments. Nonionic flocculants are employed in scenarios where charge interactions need minimal interference, such as in the treatment of very fine colloidal suspensions. They are noted for their ability to stabilize flocs, making them a preferred choice in dairy and sugar industries.
6. Biopolymer Flocculants
Biopolymer flocculants, derived from natural substances like chitosan and starch, offer eco-friendly alternatives. These flocculants are gaining popularity due to their biodegradability and low toxicity. In environmental and food-related applications, biopolymers are favorable due to their sustainable production methods and minimal environmental impact.
When selecting a flocculant, several factors merit consideration
- Water Chemistry The type and concentration of suspended solids and overall water chemistry can dictate the choice of flocculant.
- Cost Efficiency Balancing the cost of flocculant use against the treatment results is vital for financial sustainability.
- Regulatory Compliance Compliance with local environmental regulations and standards often influences the selection process.
- Process Compatibility The chosen flocculant must integrate seamlessly with existing equipment and treatment methods.
Expert understanding of flocculants and their applications is instrumental in achieving targeted results. Companies offering water treatment solutions should prioritize continuous research and development. By staying abreast of the latest advancements in flocculant technology, they ensure enhanced performance and environmental stewardship.
In conclusion,
the diverse types of flocculants provide solutions for a vast array of industrial challenges. By leveraging their specific properties and applications, businesses can optimize processes, reduce costs, and meet stringent environmental regulations while maintaining the highest standards of performance and safety.